Description
Single Toggle Jaw Crusher
These kinds of crushers are the primary crushers with well-proven designs for crushing of rocks and minerals in different sizes. Size of Jaw crushers is determined by feed opening at the top of the machine. This crusher reduces the feeding minerals by pressure. “V” shaped Fixed Jaw Plate is located on a fixed surface, and the moving jaw plate hits the rocks by the forces of toggle.
The distance between fixed and moving jaw plates, determines the discharge opening jaw or maximum size of outputs of jaw. Input rocks remain in the crushing chamber until fitting the size of opening of jaw. Discharge opening is adjustable and movement of feeding is easy. Accurate design of angle between fixed jaw plate and moving jaw plate make it easy to crush the feed material and does not let the material to throw up.
Crusher frame is made of steel plate of high strength and elasticity. Points subject to stress are reinforced with heavy ribs or made in box section.
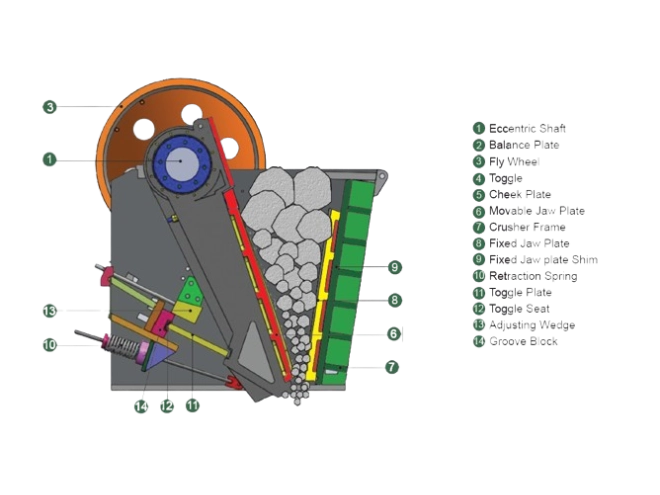
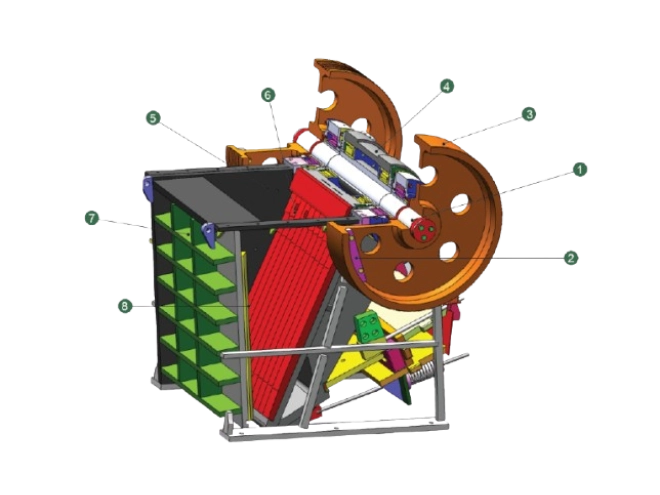
Eccentric Shaft
Eccentric Shaft of this machine is made of special high-grade forged steel and very accurately machined. The shaft is amply dimensioned and the changes between various diameters have been designed so as to reduce the danger of fatigue as much as possible.
Jaw plates
Jaw plates of this machine are made of manganese steel of great wearing strength. The backs are surface ground ensuring good contact with the frame and the moving jaw. The jaw plates are reversible, allowing full utilization. Both fine-toothed and coarse-toothed jaw plates are available.
Cheek plates
Cheek plates are also made of manganese steel. They are in two parts, so that the lower part, which takes most of the wear, can be replaced separately.
Toggle
Toggle of this crusher is made of accrete steel plates in proper thickness or made of steel casting. The proper length of toggle designing for this kind of crusher causes the best angle between fixed toggle and moving toggle, not over than standard length, so it avoids throwing rocks out.
Bearing arrangement
The roller bearings are of the spherical type which adjusts themselves to the deflection of the shaft. They are protected by labyrinth seals which are designed with minimum play and effectively pre- vent dust and dirt from penetrating into the bearings and grease from being forced out. On this crusher the frame bearings are mounted in replaceable housings which are in turn secured in re- cesses in the frame with bearing caps.
Adjusting Device
The function of the adjusting device is to compensate for wear on the jaw plates, toggle seats and toggle plate and to provide minor adjustment of the discharge opening. The adjusting wedge is raised or lowered by means of the adjusting bolts and the horizontal movement of the groove block is followed by the toggle plate and moving jaw, thus altering the discharge opening of the crusher. Adjustment can be carried out while the crusher is in motion.
For major alterations of the discharge opening, a longer or shorter toggle plate is fitted. Toggle plates are available in various standard lengths. The above methods of adjustment can be used only within certain limits. If the lower section of the moving jaw is advanced too far towards the fixed jaw plate the nip angle will be too great and the material. With the aid of a third method of adjust- ment it is, however, possible to make large alterations of the discharge opening without affecting the nip angle. This is done by inserting a thicker or thinner shim behind the fixed jaw plate. Shims are available in various standard thicknesses.
Changing the shim thickness behind the fixed jaw plate also alters the feed opening at the top. To obtain the largest possible opening no thicker shim should be used than that required with regard to a suitable nip angle.
Vertical adjustment of the Fixed Jaw plate
When altering the crusher setting the moving jaw is swung forward and upwards or backwards and downwards, thus altering the vertical position of the movable jaw plate. Faulty vertical relationship between the jaw plates will result in abnormal wear. The crushers are therefore equipped with facilities for adjusting the height of the fixed jaw plate. Adjustment can be carried out by means of levers.
Selecting jaw crusher size
Size of jaw crusher depends on desired size of feeding and its capacity. Crusher should be large enough to guarantee the average size of products. In practice, incompetent loading and other problems that may happen during the functions should be considered.
Feed opening between jaw plates should be considerably more than the largest size of rocks that enter into the crusher so that causes to reduce the danger of tumbling of disorder shaped rocks on top of the opening and not entering into the opening to crush. Materials can enter to the opening with no stop. to increase the total capacity. Size of feed opening between jaw plates are different, depends on type and condition of crushing. In a primary crusher, when the feeding includes determined rocks, controlling of roll and cubic rocks is simple than erratic rocks.
*Smaller closed side settings can be often used depending on application and production requirements For a performance estimation for your specific application, please contact Mahyar Crusher company.
**The above figures are based on feed material with an average specific gravity of 2.6, with a maximum feed size that will readily enter the crushing chamber without bridging. The capacities may very depending of the feeding method and on feed characteristics such as gradation, bulk density, moisture, clay content and crush- ability.
Reviews
There are no reviews yet.